Thermal Imaging For Steam Systems
![]()
![]()
![]()
In a 100 psig system with production costs of $8/1000 pounds, a 1/4" leak will cost $20,000 in one year and a 1/2" oriface would waste $80,000 a year.
According to the U. S. Department of Energy (DOE), more than 45 percent of all the fuel burned by U.S. manufacturers is consumed to raise steam. It costs approximately $18 billion (1997 dollars) annually to feed the boilers generating the steam. Top to Bottom’s Thermal Imaging surveys of your property’s steam and processing equipment is a cost effective program for determining the condition of the operational equipment, steam traps and piping with in the system, heat loss and equipment damage within the system that cannot be detected with the naked eye.. Our survey of a steam system can highlight the location of all areas of heat loss and process systems not performing at maximum efficiency The savings in energy and pro-longed equipment life which can be achieved by preventing such losses can be considerable. At the same time any leaks in the steam system which can be the most expensive form of energy loss can be easily identified
- Minimize Line Blockages
- Tank Level Measurements
- Improve efficiency of process systems
- Verifications of operation of all steam-using equipment
- Refractory Lining Performance
- Leak Detection
Trap Leaks/Failures
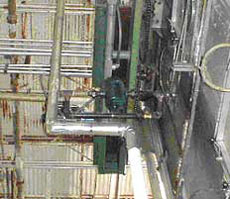
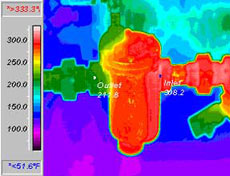
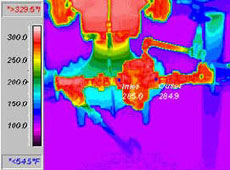
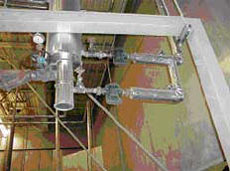
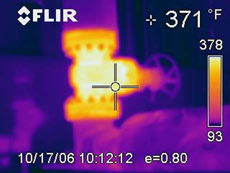
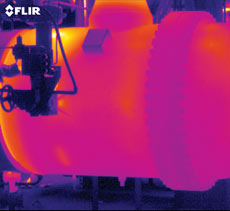
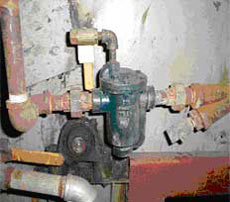
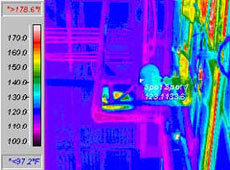
Steam trap failure can be hard to spot, but often leads to significant energy wastage and operational problems. Whether you have Float and thermostatic, fixed –orifice, inverted bucket, Float and thermostatic or thermodynamic traps in your system. Leaks in traps within a system can be equally damaging (For example, at costs of $5/1000lbs of steam a leaking trap with a 1/8inch orifice in a 50-psi system would waste 29.8lbs per hour or 260,333lb/yr. The energy waste from this trap would be $1902.00 annually. In a single system with 100 traps and an estimate failure rate of 25%, the annual cost would be $32,541 just from the traps within a steam system.) Top to Bottom’s steam trap survey program (ultrasound is also used) is an excellent addition to your company' steam system for determining the condition of steam traps, and an extremely useful part of an effective maintenance program.